External Coil Corrosion
External coil corrosion is becoming increasingly prevalent, posing significant challenges across various industries. Reasons for such corrosion range from the use of subpar copper to chemical residues left over from manufacturing processes. While some coils may arrive on-site already primed for corrosion, the majority of issues stem from environmental factors that cause corrosion to eat away at the coils from the outside in.
Case Study: A Fruit Processor’s Struggle with Corrosion
A compelling example of this phenomenon involved an American fruit processor operating in South America. Despite replacing numerous coils and employing both an internal acid detector and acid eliminator from Mainstream Engineering, the corrosion persisted. The assumption that the cause for corrosion was internal was later disproven; instead, the source originated externally, a finding that challenged the efficacy of the existing acid test methods and remediation approaches.
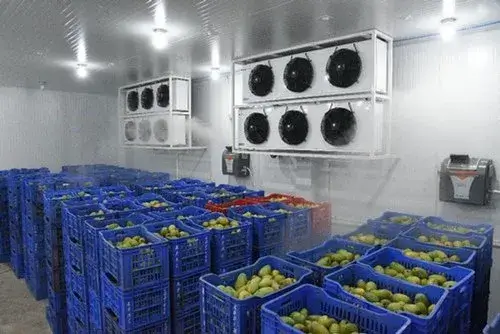
Figure 1: A Fruit Ripening Chamber
The Two Principal Types of Coil Corrosion
In fact, there are two primary types of corrosion affecting coils as noted by pervious Mainstream Material Science Engineer, Dr. Alan H Brothers.
Pitting Corrosion
Visible to the naked eye, this type of corrosion is characterized by the aggressive attack of chloride and fluoride anions on copper. Common in environments with materials like snow-melting crystals, detergents, and paint strippers.
Formicary Corrosion
This less visible form involves microscopic tunnels within the copper, resembling ant nests. It’s typically caused by organic acids found in household and industrial products.
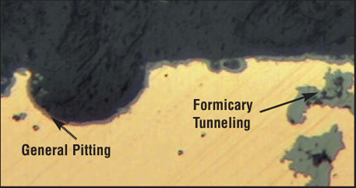
Figure 2: Pitting and Formicary Corrosion
Strategies for Prevention and Mitigation
Galvanic Corrosion
When two dissimilar metals come into contact, such as copper tubing and aluminum fins, a “galvanic couple” is formed, and the phenomenon of galvanic corrosion occurs. The presence of moisture, particularly seawater, accelerates this process by acting as an electrolyte needed in the reaction.
Keeping Coils Clean
Regular cleaning of outdoor condensing coils is vital, especially in areas prone to corrosive environmental factors. While water can be used for cleaning, specialized coil cleaners are more effective at removing existing corrosion and buildup. Coil cleaners, like QwikBright, also include a protectant in its formula to ensure long-lasting operations.
HVAC Coil Corrosion Protection
For new coils or those frequently replaced due to corrosion, protective coatings offer HVAC coil corrosion protection. Coatings such as polymers and silanes can significantly enhance the longevity and performance of coils, albeit with some potential decrease in heat transfer efficiency.
Conclusion
Understanding the specific type of corrosion and its environmental triggers is crucial for effectively managing and mitigating coil corrosion. For HVAC service technicians and engineers, this knowledge is instrumental in choosing the right strategies, from selecting appropriate coatings to implementing regular maintenance schedules, to protect and extend the life of HVAC coils. This comprehensive approach not only addresses the immediate challenges of coil corrosion but also contributes to the long-term sustainability and efficiency of HVAC systems worldwide.
Related QwikProducts
Image Sources
Figure 1: https://www.indiamart.com/proddetail/fruit-ripening-chamber-22470370373.html Figure 2: http://www.hydro-temp.com/help/drawings/Formicary_Corrosion.pdf